Litauen: DHL-Flugzeug Stürzt Ab
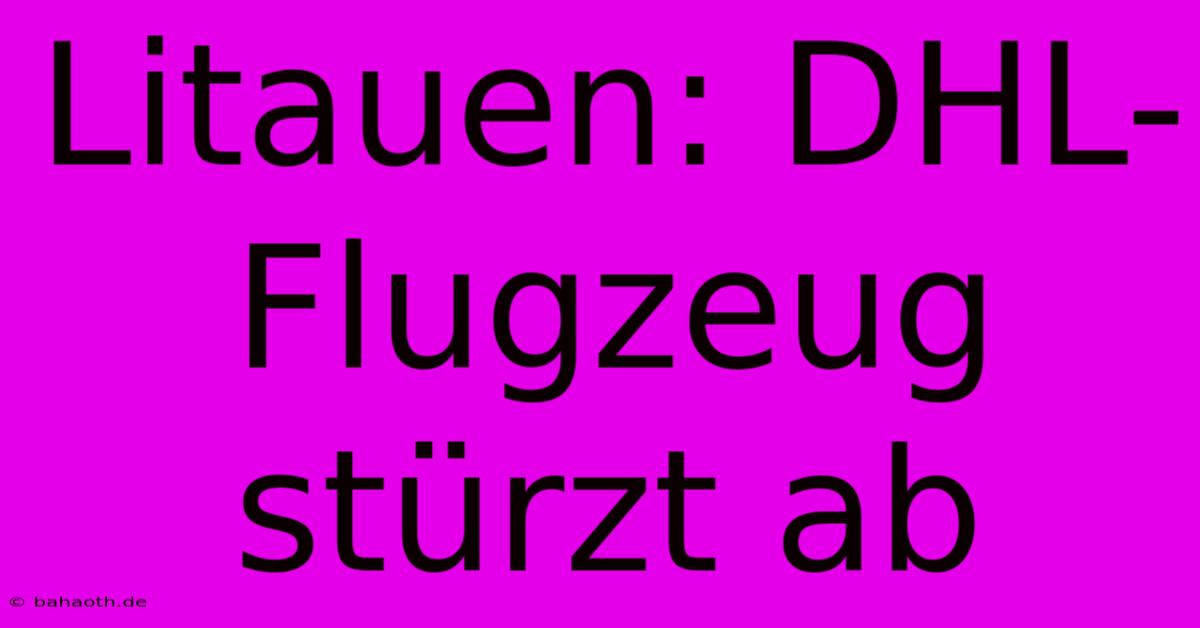
Discover more detailed and exciting information on our website. Click the link below to start your adventure: Visit Best Website Litauen: DHL-Flugzeug Stürzt Ab. Don't miss out!
Table of Contents
Litauen: DHL-Flugzeug stürzt ab – Ein Schock für die Logistikbranche
Oh man, when I heard about that DHL plane crash in Lithuania, it totally freaked me out. I mean, seriously, a DHL plane? That's like, the epitome of reliable shipping, right? To think something like that could happen… it shook me. I’ve spent years optimizing my own logistics for my online business, and seeing something like this made me re-evaluate everything.
I remember that day vividly. I was actually working on a blog post about improving e-commerce fulfillment times – ironic, huh? – when the news broke. My jaw literally dropped. My first thought wasn’t even about the potential loss of life (though obviously that’s paramount), but about the massive logistical nightmare this would cause. Thousands of packages, probably destined for all over Europe, suddenly grounded. Supply chains disrupted. Businesses scrambling. It was a total catastrophe.
The Human Cost & Logistical Fallout
The immediate impact, of course, was the tragic loss of life. My heart goes out to the families and loved ones affected. Beyond the human tragedy, though, the crash highlighted the fragility of global supply chains. We all take these things for granted – you order something online, and it magically appears on your doorstep a few days later. But it takes a massive, complex network to make that happen. And when something like a plane crash happens, the whole system can grind to a halt.
This incident served as a brutal reminder that even the most established companies are vulnerable. DHL, despite its reputation, couldn't prevent this accident. It underscores the inherent risks in air freight. This isn't just about speed and efficiency. It's about safety and redundancy, two factors often overlooked in the relentless pursuit of faster delivery times.
What We Can Learn from the Tragedy
This tragedy isn't just some grim news story; it's a case study in risk management. For me, it forced a serious rethink of my own approach. I started digging deeper into DHL's safety procedures (as much as publicly available information allows), and looking at best practices in other industries.
Here's what I learned:
-
Diversification is key: Don't put all your eggs in one basket. Using multiple shipping carriers isn't just about price comparison; it's about resilience. Spreading the risk across different airlines, shipping routes, and even modes of transport (road, rail, sea) significantly reduces vulnerability. I now use a combination of DHL, FedEx, and even some local couriers, depending on the destination and urgency.
-
Redundancy is your friend: Think about backup plans. What happens if your primary supplier or shipping partner experiences a major disruption? Do you have alternative arrangements in place? For me, this means having multiple suppliers for key components and keeping a buffer stock of crucial items.
-
Transparency is essential: This relates to both your own operations and those of your partners. You need to understand the risks involved in your supply chain, and be able to communicate those risks effectively to your customers. It's important to be upfront about potential delays.
Beyond the Headlines: A Call for Enhanced Safety
The Lithuanian DHL crash serves as a somber reminder that the pursuit of efficiency shouldn't come at the expense of safety. Regulations need to be rigorously enforced, and continuous improvements in aircraft maintenance and pilot training are vital. It’s not just about the immediate impact; it’s about long-term change to prevent such tragedies from happening again. Let's hope this terrible event leads to positive changes within the aviation and logistics industries.
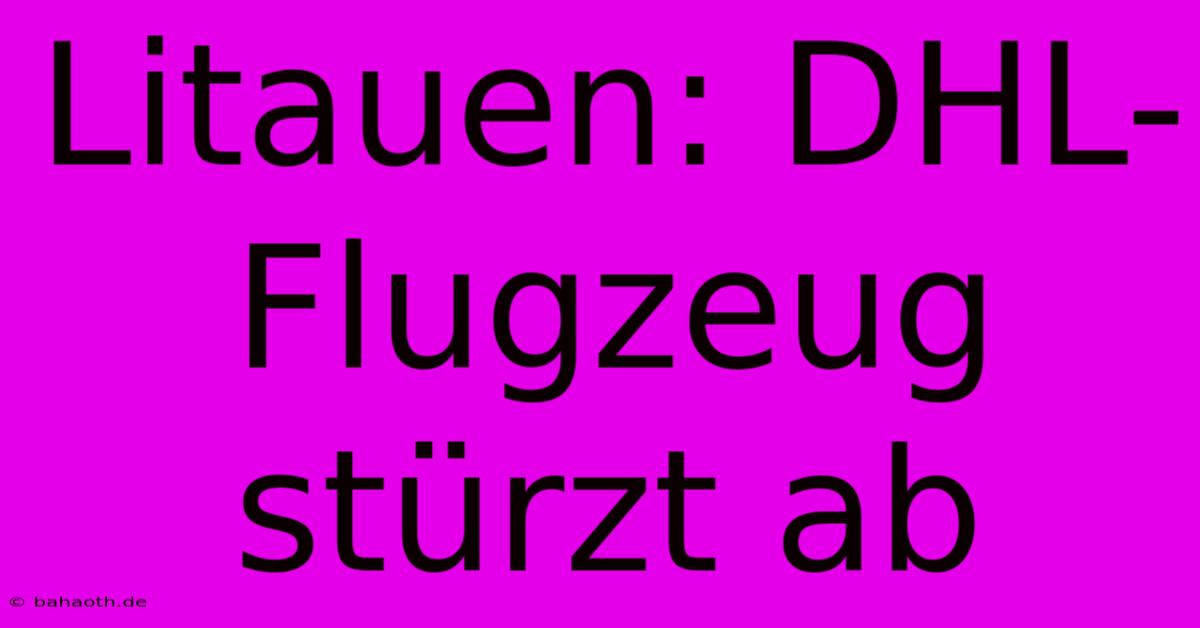
Thank you for visiting our website wich cover about Litauen: DHL-Flugzeug Stürzt Ab. We hope the information provided has been useful to you. Feel free to contact us if you have any questions or need further assistance. See you next time and dont miss to bookmark.
Featured Posts
-
Airpods Pro 2 Deals Vor Black Friday
Nov 26, 2024
-
Uruguay Rueckkehr Der Linken
Nov 26, 2024
-
Haaland Gefaengnis Wegen Mini Summe
Nov 26, 2024
-
Walliser Lokale Raclette Im Sinkflug 36 Zeichen
Nov 26, 2024
-
Kanzlerkandidat Spd Waehlt Scholz
Nov 26, 2024